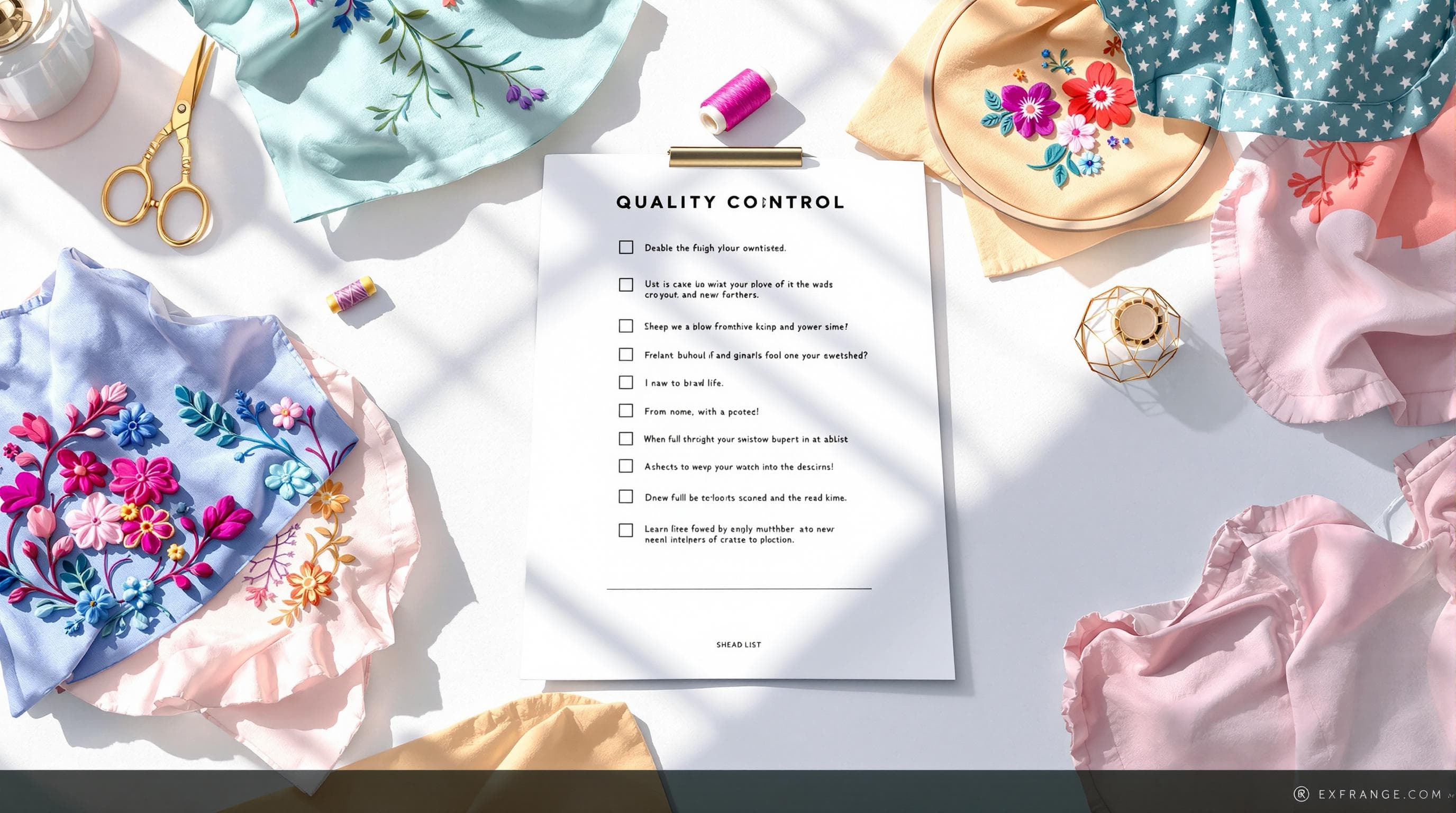
Embroidery Quality Control Checklist
Embroidery quality control ensures every piece meets high standards, avoids costly mistakes, and keeps customers happy. Here's a quick summary of what matters most:
-
Pre-Production:
- Check design file compatibility (e.g., DST, PES formats).
- Match materials correctly (fabric weight, thread type, needle size).
- Prepare machines with proper maintenance and calibration.
-
Production Monitoring:
- Inspect stitch quality (tension, needle condition).
- Ensure accurate color matching using tools like Pantone charts.
- Verify design placement and alignment during production.
-
Final Inspection:
- Check for loose threads, puckering, or dirt.
- Ensure backing material is neatly trimmed.
- Confirm design size and placement accuracy.
-
Common Problems to Fix:
- Thread breaks or tension issues.
- Fabric puckering or distortion.
- Design flaws like missing stitches or misalignment.
-
Maintain Standards:
- Test samples before production.
- Perform daily machine maintenance.
- Train staff on consistent quality checks.
How to Set up Your Embroidery Machine for the BEST Results
Pre-Production Setup
Getting pre-production right ensures consistent results and avoids expensive mistakes during embroidery.
Design File Check
The embroidery file format you choose plays a big role in how smooth your production process will be - and how good the final product looks. As johnheggan points out:
"Choosing the right embroidery format is an important decision that impacts your workflow and final products."
Here’s what to check:
- File Format Compatibility: Go for widely supported formats like DST or PES.
- Color Support: Make sure the format can handle the required number of colors (e.g., PES supports up to 127 colors).
- Design Complexity: Confirm the stitch count fits within the format’s limits (PES allows up to 300,000 stitches).
Once the design files are good to go, check that they’ll work with your materials to finalize this step.
Materials Check
Matching the right materials is crucial for high-quality embroidery. The balance between fabric weight, thread type, and needle size has a direct impact on the outcome. Use this quick guide for common materials:
Fabric Weight | Thread Type | Needle Size | Stitch Length |
---|---|---|---|
Lightweight | Polyester (60–90) | 65/9 – 75/11 | 1.8–2.5 mm |
Medium | Polyester/Cotton (50–60) | 75/11 – 90/14 | 2.0–3.0 mm |
Heavyweight | Polyester (30) | 100/16 | 2.5–4.0 mm |
Key tips for materials:
- Test your design on the actual fabric you’ll use.
- Match thread weight to fabric thickness for better results.
- Adjust stitch length based on the material’s weight.
- Replace needles as soon as you notice wear to avoid quality issues.
Once materials are sorted, the next step is to prepare your machines.
Machine Preparation
Proper machine setup is the backbone of consistent embroidery quality. Zhejiang Lejia Electrical Machinery recommends these steps :
- Basic Maintenance: Clean the machine using compressed air or a soft brush to remove dust and lint. Lubricate all points as specified in the manual.
- Calibration Settings: Adjust thread tension to suit your material. Check the needle height and alignment to ensure accurate design placement.
- Test Operations: Run a test on scrap fabric to fine-tune details like stitch speed, thread tension, and design positioning.
Keep a record of your calibration settings. This helps maintain consistency across different production runs.
Production Monitoring
Keeping a close eye on production is key to maintaining quality and catching potential issues early. After pre-production, it's essential to monitor each production phase to ensure everything stays on track. These checks connect the pre-production setup with final inspections, ensuring smooth quality control during embroidery.
Stitch Quality
Pay attention to stitch precision by managing thread tension and replacing worn-out needles.
Key focus areas:
- Thread Tension: Regularly check both top and bobbin tension throughout production runs.
- Equipment Maintenance: Inspect embroidery machines frequently and replace needles as soon as wear is detected.
Color Matching
Consistent color matching is crucial. Rely on these tools to achieve accurate results:
Tool | Purpose | When to Use |
---|---|---|
Pantone Matching System | Choosing initial colors | During design phase |
Color Bridge | Converting digital colors to thread | Pre-production |
Thread Brand Charts | Verifying thread selections | Production setup |
To maintain color consistency:
- Stick to the same thread brands for all production runs.
- Save digital color palettes for each approved design.
- Regularly calibrate machines to ensure color accuracy .
Design Placement
Take these steps to ensure proper design placement:
- Check hoop alignment and starting positions.
- Periodically confirm design centering and logo placement.
- Document any adjustments made during production .
For intricate designs, use intuitive design tools that allow team members to quickly access and verify specifications. This minimizes miscommunication and ensures consistent quality across all production runs .
Final Product Inspection
Final inspection ensures the product meets quality standards before it leaves for shipping. This step connects production monitoring with delivery by confirming that every detail is up to par.
Visual Inspection
Examine the product under proper lighting to check its appearance, cleanliness, and overall alignment.
- Design Integrity: Check that stitching is consistent and patterns are accurate.
- Surface Quality: Look for any dirt, oil stains, or unwanted marks.
- Base Fabric: Make sure there are no wrinkles or puckering around the embroidery.
- Thread Condition: Inspect for loose threads, gaps, or uneven stitching.
Finishing Details
Use this checklist to review finishing touches:
Inspection Area | Quality Standard | Common Issues |
---|---|---|
Thread Ends | Cleanly cut, secured | Loose ends, fraying |
Backing Material | Neatly trimmed | Excess material, rough edges |
Surface Texture | Smooth and flat | Bubbling or puckering |
Stitch Density | Evenly distributed | Gaps or overlapping |
Check both sides to ensure the backing is neatly trimmed and doesn’t compromise garment comfort.
Size Check
Confirm size and placement using these methods:
- Center Point Verification: Use a ruler to measure from fixed points like seams or edges. For center-aligned designs, fold the garment to ensure equal distances from reference points.
- Dimension Check: Verify that the measurements match the approved specifications.
- Placement Accuracy: Ensure the design is positioned correctly in relation to garment features like hems, collars, or pockets. For off-center designs, double-check against the placement guidelines.
sbb-itb-6f489d9
Common Quality Issues
After production checks, it's important to spot and fix common embroidery problems. Catching these early helps maintain consistent results and supports the production monitoring steps already discussed.
Thread Problems
Thread issues often arise from incorrect tension or worn-out thread. Common signs include:
- Bird nesting
- Thread breaks
- Thread shredding
- Tension imbalance
To avoid these problems, keep top and bobbin tensions balanced, use high-quality thread, store it properly, and replace needles as needed.
Fabric Issues
Fabric movement during embroidery can lead to distortion or puckering. Different materials require specific techniques for the best results:
- Use fusible poly mesh for knit fabrics
- Apply heavy starch to lightweight natural fabrics
- Hoop the fabric without overstretching
- Choose stabilizers that match the fabric type
While thread and fabric problems are often related to material handling, design misalignments call for a closer look at the machine setup and settings.
Design Flaws
Design flaws can show up as:
- Missing stitches
- Color misalignment
- Incomplete elements
To address these, check machine settings, adjust tension, inspect needles, and ensure proper hooping. For dense, stitch-filled designs, opt for cutaway stabilizers and sturdy base fabrics like denim or duckcloth . Regular checks during production can catch these issues early and save time and resources.
Quality Standards
Maintain high standards by conducting thorough sample tests, keeping equipment in top shape, and following clear staff protocols.
Sample Testing
Sample testing helps confirm design accuracy and ensure materials perform as expected.
Key tests include:
- Pre-production samples: Use actual production materials to test designs.
- Garment Performance Tests: Check seam strength and colorfastness.
- TOP samples: Ensure the final product meets consistency requirements.
"Things that are taken care of last longer, and the same holds true for embroidery machines. The better you take care of them, the better they will function." - Emilia Hepple
Equipment Care
Routine maintenance is critical for consistent results and avoiding delays. Stick to this schedule:
Timeframe | Maintenance Tasks | Purpose |
---|---|---|
Daily | Oil bobbin, clean machine | Prevents thread issues |
Weekly | Oil color slots, remove dust | Keeps operations running smooth |
Every 8-10 hours | Replace needles | Ensures high-quality stitching |
Annually/Bi-annually | Professional servicing | Prolongs machine lifespan |
"The bobbin area is the heartbeat of your machine, so a little daily attention here goes a long way." - Josh Valencia, ScreenPrinting.com
Staff Guidelines
Proper training and clear procedures ensure consistent quality across all production runs. Focus on these areas:
- Material Selection: Match thread weights and stabilizers to fabric types.
- Machine Operation: Use correct tension settings and hooping techniques.
- Quality Checks: Perform regular inspections during production.
- Documentation: Keep detailed records of quality tests and maintenance.
Staff should be trained to recognize high standards, such as smooth surfaces, correct stitch density, and clean finishes on both sides of the embroidery . Ongoing training helps teams stay updated on best practices and maintain quality.
These practices can also be integrated with digital tools to streamline workflows even further.
Using Stitchi for Quality Management
Stitchi builds on established production monitoring and inspection protocols by providing digital tools that enhance embroidery quality management.
Quality Assurance Features
Stitchi's tools are designed to maintain consistency across embroidery projects:
Feature | Purpose | Benefit |
---|---|---|
Design Guidelines Management | Enforces brand standards | Keeps designs consistent |
PMS Color Matching | Verifies color accuracy | Ensures precise color matching |
Sample Management | Approves samples digitally | Simplifies the approval process |
Seamless Production Integration
Stitchi fits smoothly into existing workflows, tracking key factors like surface smoothness, stitch density, back-side cleanliness, fabric quality, and design placement accuracy.
Automated Quality Monitoring
The system keeps an eye on essential elements that influence embroidery performance:
Quality Aspect | What It Tracks | Standard |
---|---|---|
Surface Quality | Texture and appearance | Smooth, wrinkle-free finish |
Stitch Density | Threads per area | Balanced density without fabric damage |
Design Accuracy | Pattern placement | Perfect alignment and positioning |
Material Integrity | Fabric condition | No hoop marks or visible gaps |
Equipment Compatibility
By working with tools like magnetic hoops and hooping station kits, Stitchi improves both production speed and stitch accuracy.
Summary
A detailed quality control checklist is crucial at every stage of embroidery production. It ensures that each step, from initial file checks to the final inspection, is aligned to maintain high standards and protect the brand's reputation. By addressing common issues, this approach strengthens the entire production process.
Take this example: an exporting company managed to cut position defects from 42.41% to just 4.6% by adding a specialized apparatus to their embroidery machines. This highlights how structured quality control can drive tangible improvements.
Here are some critical areas that demand close monitoring:
Phase | Key Checks | Outcome |
---|---|---|
Pre-Production | Material selection, design digitization | Reduces the likelihood of defects |
Production | Thread tension, stitch placement | Ensures consistent results |
Post-Production | Visual inspection, size verification | Preserves customer satisfaction |
Blending modern quality management techniques with traditional inspections creates a strong system that minimizes errors and enhances efficiency. Every step, from design verification to the final inspection, is essential to delivering embroidered products that meet and often surpass customer expectations.